Summary
The industrial scenario is going through a profound transformation that requires a new way of thinking, flexibility and attention to sustainability. Neo-industry values training combined with technological innovation and promotes the constructive union between people and machines.
-
BY PARTICIPATING
The painful but constructive ruptures of the new industry
-
BY PARTICIPATING
Find out how and when to request reimbursement for medical expenses
-
BY PARTICIPATING
He came from Portugal to start a business in SP. And it has borne great fruit!
-
BY PARTICIPATING
Concerned parents undertake vaccination and hope to earn R$44 million
New behaviors, disruptive technologies, accelerated speed of information and actions, new generations entering the job market in a convergent way – or not! – with the most experienced, constant and globalized changes, in addition to the great global attention to sustainability – of the planet and of business. The industrial scenario is going through a moment of transformation, which requires a new way of thinking from the market and professionals, much more outside the box, with flexibility and availability.
The economy continues to be driven by industrialization, but now in a 5.0 society. This is a breakdown of concepts that will probably be painful at first, but which, in the long term, will be responsible for significant changes, as is already happening in the so-called neo-industry: the digital, humanized, innovative and clean industry.
This breaking of paradigms should, in the long term, lead to collective, sustainable and long-lasting improvements. Until then, it is necessary to find solutions that, on the one hand, facilitate and integrate digitalization and artificial intelligence into industrial processes and, on the other hand, develop the people capable of managing them. Today what we see, especially in Brazil, is a generation that devalues technical and operational positions. It is true that, with technology, the number of people engaged in industrial operations has decreased significantly, however we still need specialized professionals who know how to use new intelligent equipment.
So much so that from a survey conducted in this first semester by the National Confederation of Industry (CNI) it emerges that the main investment objectives planned by the industry for this year have risen to 73% in 2024 compared to 68% in 2023 , are focused on expanding or improving technical capacity and manufacturing process, both were the choice of 42% of the 381 large companies consulted. In other words, the machine does not overlap with man, on the contrary, its effectiveness depends on the evolution of human intelligence!
This is a mission that must be embraced by People Management, the former HR, which, with home office and remote working, encounters difficulties in finding professionals and, subsequently, in retaining them. More than just supporting payroll or employee benefits, people management must be a strategic area of knowledge management. It is clear that it is necessary to prioritize investments in technical development, but not only from a career development perspective, but also to incentivize digital transformation and social and working environment well-being. Human resources are the foundation between people and machines, promoting a constructive union between technology, people and industry.
It is here that the role of industry converges with the broader concept of sustainability, which does not consider environmental responsibility, but also social and governance responsibility. Training combined with technological innovation contributes significantly to energy efficiency, the objective of the strategic actions of globalized companies. In 2023, 78% of Brazilian companies invested in technological progress, 58% in human development and 34% associated these investments with concern for environmental impact.
The numbers reveal the movement towards industrial disruption and, with it, the evolution of its global impact. Although the sector is used to creating compositions in transformative scenarios, at the moment it is difficult to consider all aspects: there is a lack of energy, the turnover of people is increasing, we are subject to the invasion of information systems. The speed with which innovations develop and the global communication that allows an idea to be conceived in Paris, developed in Beijing and delivered for testing in Los Angeles, makes the market much more transparent and faster, with no room for so-called “secrets”. “industrial” which lost its value and became almost folkloristic. Therefore, the need to think differently, act differently and expect different results.
The new industry must not only deal with producing products, but must start offering support for their use by the customer. Today, flexibility and the willingness to help customers improve their processes through product development is a dominant factor in the industry. This requires speed and efficiency to develop testable prototypes in days or even hours. And this involves the interaction of internal staff with the customer and the market. You need to know to develop and evolve.
Finally, accepting this brokenness and thinking differently does not depend on age or generation, but on accepting the risk of doing things right or wrong. Half of the ideas will work, the other half won’t, the difficult thing is knowing which one to bet on.
Andreas Göhringer is director of the German multinational Gemü Brasil.
Source: Terra
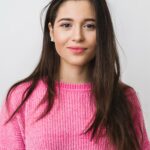
Rose James is a Gossipify movie and series reviewer known for her in-depth analysis and unique perspective on the latest releases. With a background in film studies, she provides engaging and informative reviews, and keeps readers up to date with industry trends and emerging talents.